The machining settings are general settings related with the gcode output or methods of machining and their options/variations.
m.1) Spindle
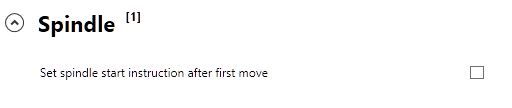
This option forces that the spindle starts after the first cycle movement. Example below:
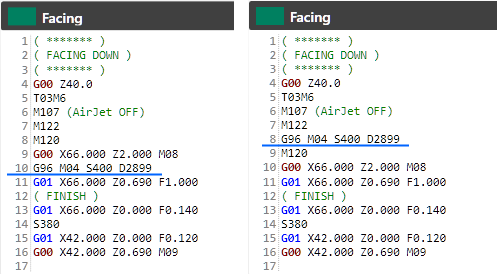
m.2) Tool selection
Tool selection menu depends on the cycle type so that individual options are better structured
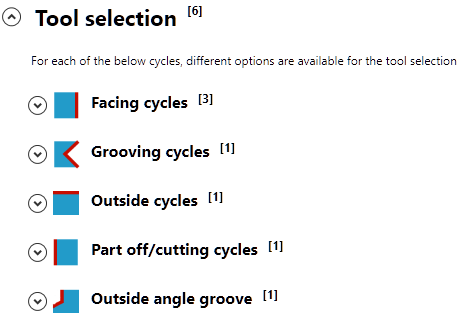
Facing cycles
a) Use groove tools also for facing operations
The facing tools are generally only used to do facing operations. The same happens with the grooving tools, they are used on grooving operations. With the option enable, on a profile that has both a groove and a facing, try’s to use the same groove tool also on the facing operations. As a advantage, this option will make less tool changes but will use more expensive tools (groove vs facing that is a less expensive tool)
b) Select facing tool not based on priority only but taking in consideration the tool that can reach more precisely the final toolpath
Using this option both the priority and the radius of the tool are considered to better match the final tool path. For example, if the facing shape contains radius of 0.5mm it is better machined with a tool that has a radius 0.4mm than with a tool with radius 0.8mm.
c) Select groove tool R0.4 on facing operations
This option try’s to force the selection of the groove tool with the radius more close to 0.4mm (generally available among suppliers) to be used in all facing operations that match the options selected. The options are based on diameter and material type.
Setting the diameter as 0, will disable the option.
Grooving cycles
a) Lower limit of front grooves set to 0.4mm
This option is described on the following page: Lower limit of front groove
Outside cycles
a) Preferably use tools for polymers before machining.
This option was introduced to use the polymers tools on materials of the rubber group. On rubbers, that generally have a protective cover on the outside, that can be more aggressive for the tool durability, when enable, this option will automatically select – when possible – the outside polymers tools to make the rough machining. The finish machining will still be done with the elastomers tooling. Only the outside is affected.
If the amount of material to remove is small the option will be automatically discarded.
Part off/cutting cycles
a) Preferably use soft part off tools in PTFE parts with cross section less than
On PTFE profiles with a small cross section is possible to use the soft part off (chip less cut) part off. The soft part off has a width of 0 mm and therefor will have a smaller waist of material, but at the same time it cannot be used on a thicker material.
With this option, the user can select the desired cross section to use this option. Setting it as zero (0) the option will not be used.
Outside angle groove cycles
a) Use groove tools also for facing operations
On this menu a option is present to enable the machining of the angle outside grooves using the o’ring tools that have the corresponding option active. To enable generally this option the checkbox present on this menu must be active. When this option is active the software will try to use the orings tools where the user selected as able to machine the angle grooves.
See more in: https://www.fastseal.eu/blog/oring-tools-grooves-with-angles
m.3) Path
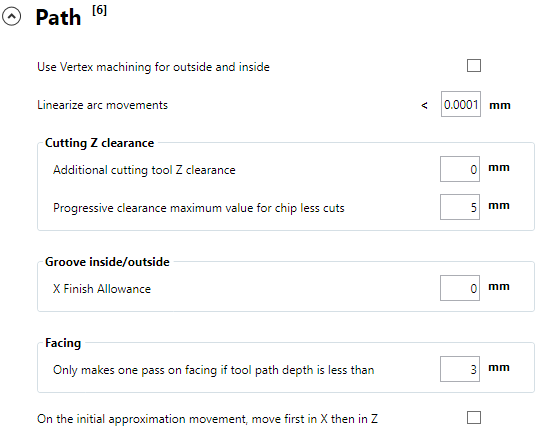
The path selection options are as follows:
m.3.1) Use vertex machining for outside and inside
Vertex machining is a method to leave sharper edges on some profiles. The difference on the machining with the option on and off is as shown on the image below.
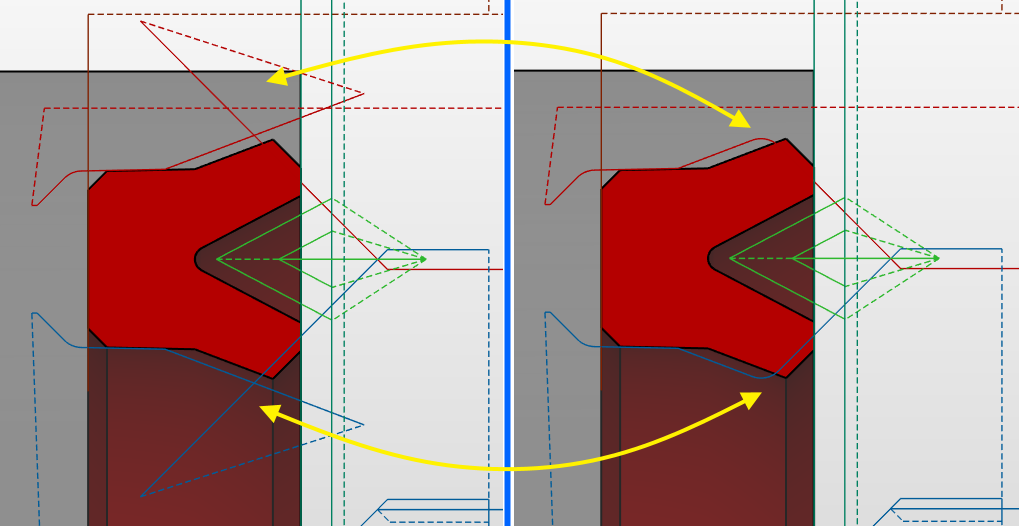
With the vertex option on, there is a intersection movement of the tool to make a sharp edge on the resulting shape. With the option off, the machining is standard, where the tool follows the initial path, being always in contact with the final shape.
m.3.2) Linearize arc movements
This sets the size from which any arc will be treated as a line. If the value is for example 0.001, it means that any arc witch its length is smaller than 0.001 will the transformed to a line on the output code.
m.3.3) Cutting Z clearance
On the cutting Z clearance, some control is provided to the user to set how the Z clearance is managed. The Z clearance can be resumed to the space left after the part ends, and the amount of material that is machined to provide space for the cutting tool. Internally a minimum amount is already added to provide a safe margin of cutting amount, that can be larger using the following options:
m.3.3.1) Additional cutting Z clearance
This setting will add a fixed value to the prebuild value present on the software.
m.3.3.2) Progressive clearance maximum value for chip less cuts
This setting only affects the elastomers part off (chip less part off), and it attempts to increase the clearance based on the thickness amount to cut. As the chip less cutting tool have its body more thick at the tool base, more thick cuts also need more clearance so that the tool can fit on the material to cut.
The value on the setting will correspond to the maximum clearance amount that is calculated at 55mm cross section cuts. As a example, if the setting is 6mm and the cut has a cross section of 22.5mm, the additional clearance will be 3mm.
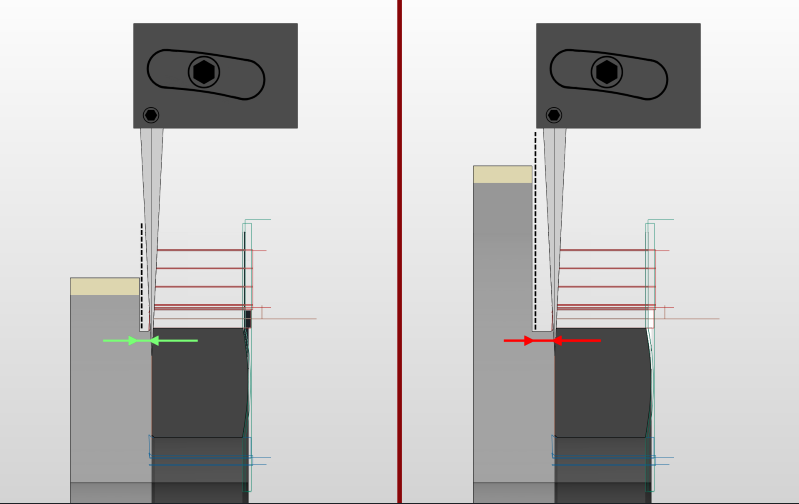
m.3.4) Groove inside/outside – X finish allowance
This informs the software about the amount that should be used for a finish pass on groove operations.
m.3.5) Only makes one pass on facing if tool path depth is less than
This option is described on the following link: Ignore facing roughing
m.3.6) On the initial approximation movement, move first in X then in Z
This option is described on the following link: Approximation movement
m.4) Cycle preparation
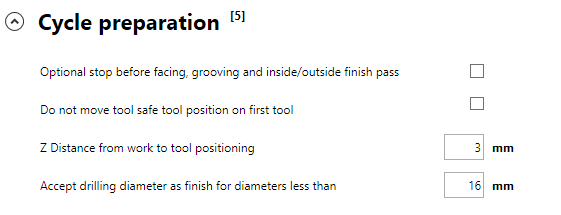
m.4.1) Optional stop before facing, grooving and inside/outside finish pass
As the option states, with this option on, a optional stop code (common M01) will be added before the finish passes of the listed cycles.
m.4.2) Do not move tool safe position on first tool
The save movement is not performed on the first tool. It will still be done on the remaining tools.
m.4.3) Z distance from work to tool positioning
When the tools move in rapid movements before starting to machine, they normally move to a Z=2, meaning that the tools will be away from the material for a amount of 2mm. This value can be changed on this setting.
m.4.4) Accept drilling diameter as finish for diameters less than
When a drill is used, there will be no inside machining if the drill diameter is less than the value placed by the user. Examples: if the setting is 16mm and a seal with a 6mm diameter is asked for, and if a drill of 4mm is used, no inside machining will be used. For the same example, if the setting was 5mm, the inside machining would exist.
m.5) Split default values
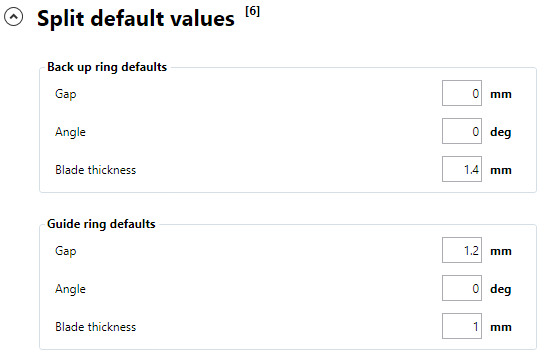
For split parts, like guide rings or backup rings, there are extra options for the desired gap and angle of the cut.
On this settings the default values can be set, as each company might desire a standard gap and cutting angle different from others. Also the blade thickness to be used can be set. Example of a guide ring with 1.2mm as gap, 1.4mm as blade and 10ยบ for the angle:

m.5.1) Gap
Desired space between the two faces of the cut. Set in mm.
m.5.2) Angle
Desired cutting angle, set in degrees. Refer to image to verify from what face it is measured.
m.5.2) Blade thickness
Blade thickness used to perform the cuts.