To add or edit materials, the following window is used:
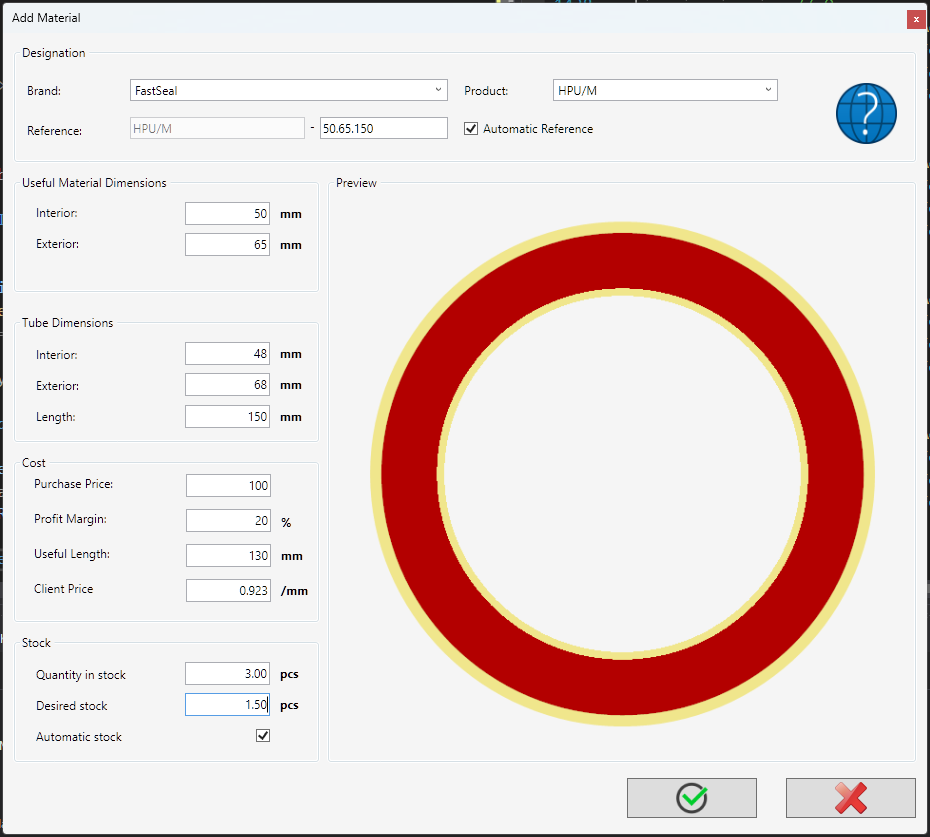
Each option is explained in detail below:
Designation group
Brand: Brand of the product to be added. It must be one of the brands already on the system
Product: Selection of the product to be added. It must be one of the products already added on the system
Reference: If the automatic reference is selected (highly recommended) then the software will generate one reference that is easy to read and that makes use of the inside, outside and length of the tube.
Useful material dimensions
As the group name informs, the dimensions here refer to the useful material dimensions, that are by norm the ones on the supplier sticker
Interior: Inside useful dimension of the material to be added. Can be zero for solid materials.
Exterior: Outside dimensions of the material being added.
Tube dimensions
Differently from the useful material dimensions, the tube dimensions refer to the actual measured dimensions. For example, NBR tubes have a protective cover that makes the tube much larger than the actual useful dimensions. This measured, larger dimension is to be added here.
This dimensions cannot exceed the useful dimensions.
Interior: Inside measured dimension of the material to be added. Can be zero for solid materials.
Exterior: Outside measured dimensions of the material being added.
Note that on the graphical representation, the inside and outside excess are represented by a yellow region.
Cost
On this group cost related settings are added and will be used to calculate the material cost on quotations and on final prices. There is no specific currency to be used, the user is free to use its currency.
Purchase price: Cost of the full tube/material
Profit margin: Extra % amount to be added into the tube cost
Useful length: Total length in mm that can be used from the material being added. Normally on a 150mm tube, around 130mm can be used as the remaining will be waist.
Client price: Based on the previous values, the software presents a calculation per mm of the material cost for the client
Stock
On this group the material stock and stock related options can be changed.
Quantity in stock: Current stock of the product. Values can use decimals. For example 2.5 means two and half tubes in stock
Desired stock: For each material in stock a determined amount can be set that sets the desired stock. This value is meant to represent a stock quantity (measured in tube quantity) that reflects a stable stock. This value will then be a indicator of the stock level, that can be seen on the material list or on the reports, that was implemented to help the users to order material.
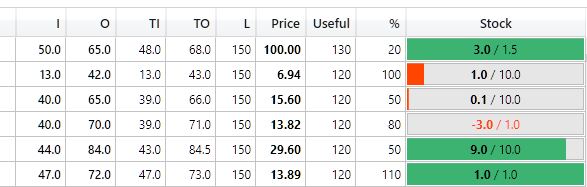
Automatic stock: If this setting is not checked/on, when a seal is made that uses this material, the stock will not be changed and all stock management must be made manually. If the option is set, when a seal is made, the calculated quantity will be deducted from the stock. In any of the options, the stock can be manually changed at any time.
Change stock management for all materials
It is possible to set automatic or manual stock management for all materials on the database. To do so, log in as root and access the “Database maintenance” on the settings menu:
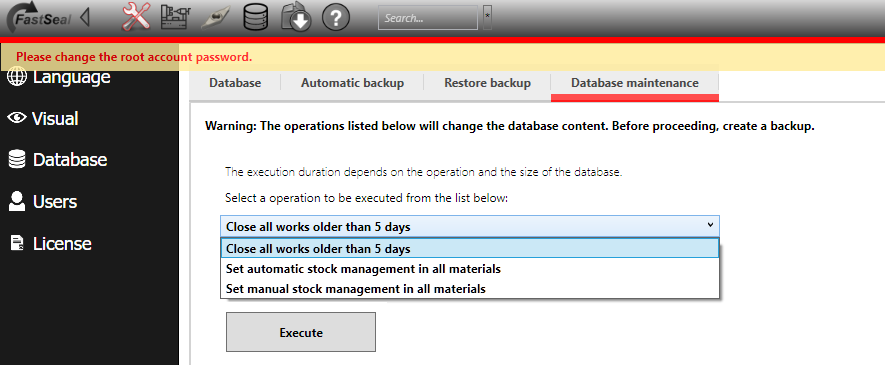
Choose the desired option and press execute.
If the material database is open it must be reopen (simply navigate to another database page, then open again) to the stock management for each material to be visible.